Rio Wil
|
 |
« on: September 30, 2013, 05:06:12 PM » |
|
I called Drive Line Express in Redding, CA to order one of their upgraded ujoints and they said they were not going to be doing any more. The volume was just too low to justify the set up costs so its a done deal. I said I wasn't going to do this but based on the above I guess I will take on the project and see if I can make one. Not going into production, but will make one. I had a spare from eBay that was in pretty good shape, it had a tiny click that could be felt by chucking one end up in a vise and attempting to rotate the other end with a pair of channel locks. All four of the cups were nice and tight in the yoke so the yokes should be usable. The below pictures are the start of the project and I am ordering the Precision Universal #392 today from some where on the internet and have it delivered. So the yokes are pretty much ready to make the cut on the inside of the yoke where the c clips will reside....probably will just grind the flats rather than try to cut them, but will have to whip up some sort of jig to hold them, probably mount on a rotary table so I can be sure to get a perfect 180 degree rotation to make the second cut and insure both cuts are parallel. 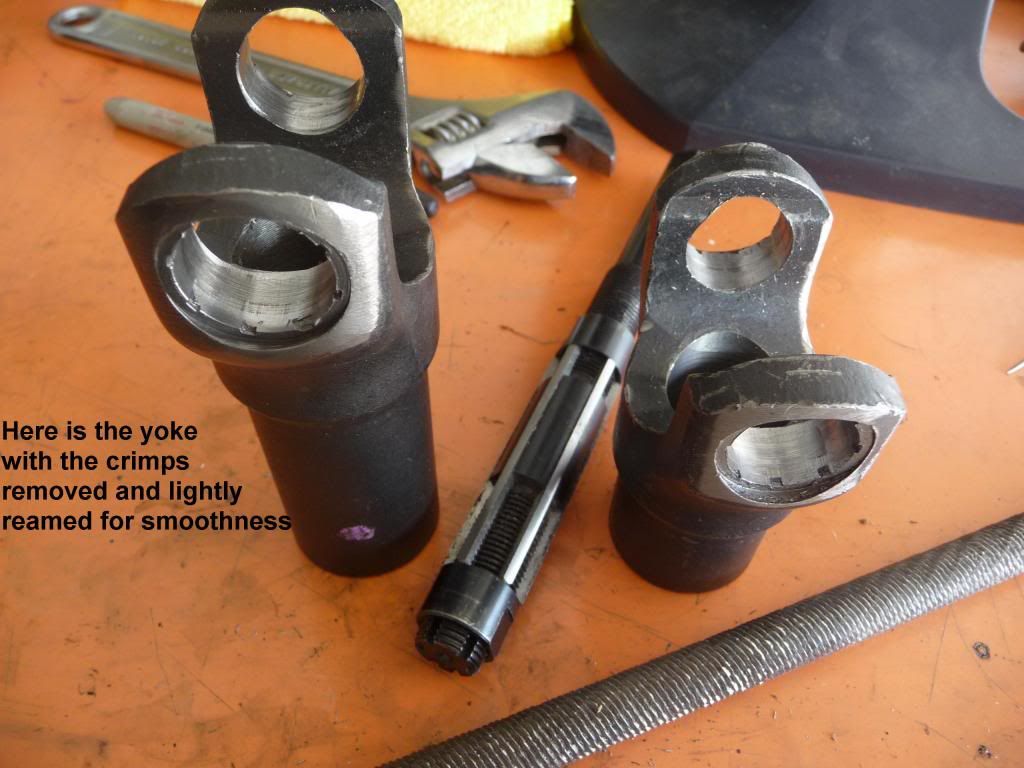  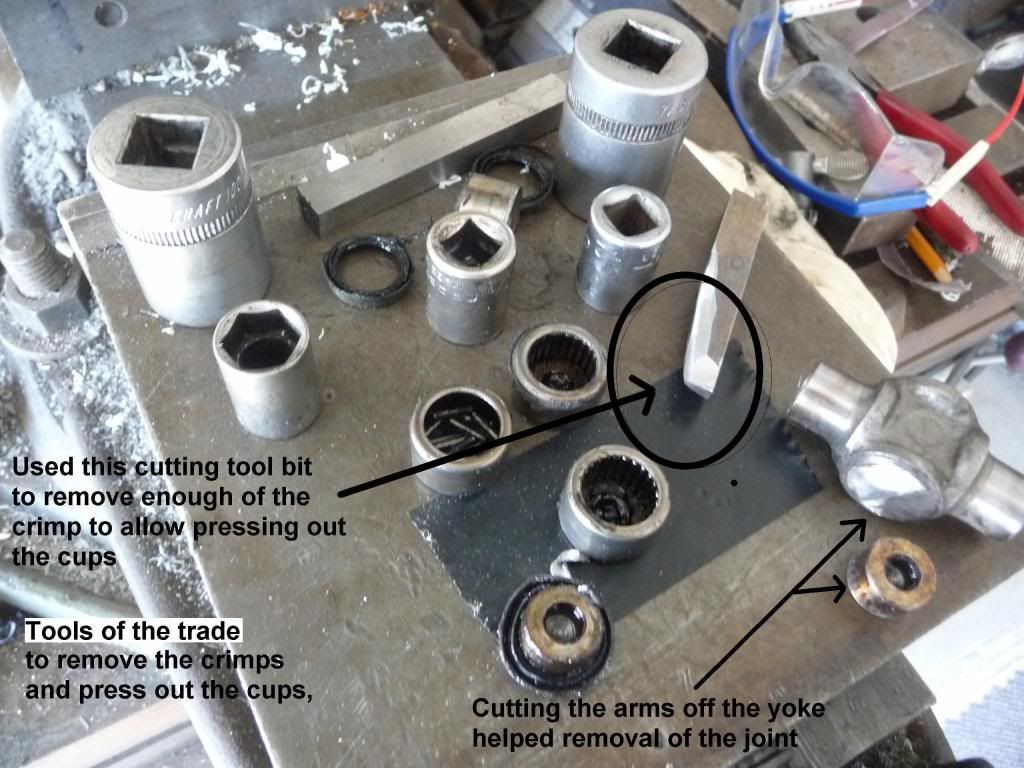
|
|
« Last Edit: September 30, 2013, 06:37:27 PM by Rio Wil »
|
Logged
|
|
|
|
pancho
|
 |
« Reply #1 on: September 30, 2013, 07:57:07 PM » |
|
Hey,,,,,, now you're talking..... I sure would like to see what kind of setup you had to remove the crimp material with that cutting tool?
|
|
|
Logged
|
The most expensive things you will purchase, are those things you would not have needed if you had listened and obeyed.
|
|
|
Rio Wil
|
 |
« Reply #2 on: October 01, 2013, 07:54:44 AM » |
|
Removing the crimp was pretty low tech....just ground a cutting edge on the tool bit and used a small hammer to gently tap each crimp from both sides and essentially shaved them off.... 
|
|
|
Logged
|
|
|
|
pancho
|
 |
« Reply #3 on: October 01, 2013, 11:05:06 AM » |
|
Yeah, I saw that was a tool you ground out of a piece of HSS, I thought it was for a lathe..... looks like it all cleaned up nicely after the pass with the adjustable reamer. Good start
...... I was picturing a complicated clamp up job on a face plate,, trying to get it centered perfectly so the crimps could be cut out on a lathe, you know, three hours of work to do a twenty minute job .........
|
|
|
Logged
|
The most expensive things you will purchase, are those things you would not have needed if you had listened and obeyed.
|
|
|
Rio Wil
|
 |
« Reply #4 on: October 02, 2013, 08:36:45 AM » |
|
Yeah, set up time can be a bear for just a couple of minutes of cutting.....thought about grinding a end mill down to the right size and do it on the mill but I didn't want to risk enlarging the bore at all. The cups on the new joint are a little taller and removing the crimp allows using the extra support available in the bore....that is if you don't enlarge the bore in that crimp area while removing the crimp....... I am going to have to make a fairly sturdy jig to hold the yoke for grinding the inner surface of the yoke to dimension and insure it is in line with the spline bore and perpendicular to the joint bores and blah blah blah.... 
|
|
|
Logged
|
|
|
|
pancho
|
 |
« Reply #5 on: October 02, 2013, 08:38:45 PM » |
|
Sounds like fun,,, post plenty of pictures as you move along.
|
|
|
Logged
|
The most expensive things you will purchase, are those things you would not have needed if you had listened and obeyed.
|
|
|
Rio Wil
|
 |
« Reply #6 on: October 04, 2013, 02:07:24 PM » |
|
This is a continuation of the previously posted 3 photos....... Need a simple method of making a jig to hold the yoke reliably on the rotary table.....this big ass bolt should do....  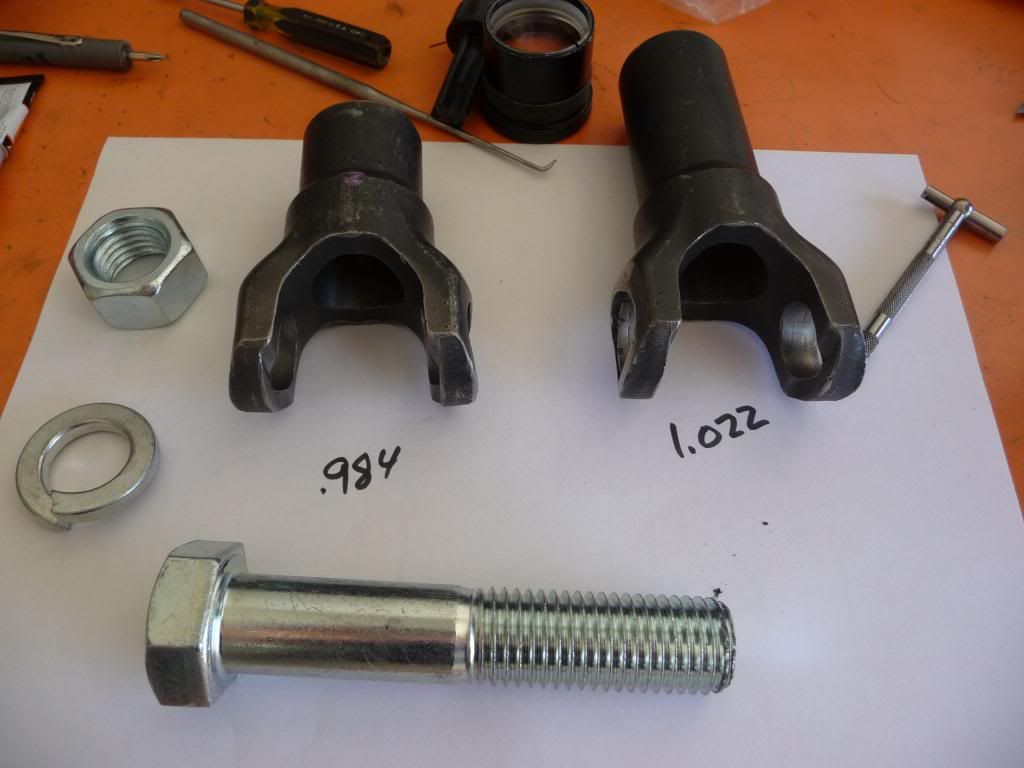 Needs a bit of reshaping.....the head will grip the splines inside the bore   Fits nicely......  The hole in the rotary table is a bit big so I need a slightly tapered bushing to take up the slack abd center the yoke perfectly..   Made it out of aluminum ........and while on the lathe, files a slight bevel to match the table bore.. 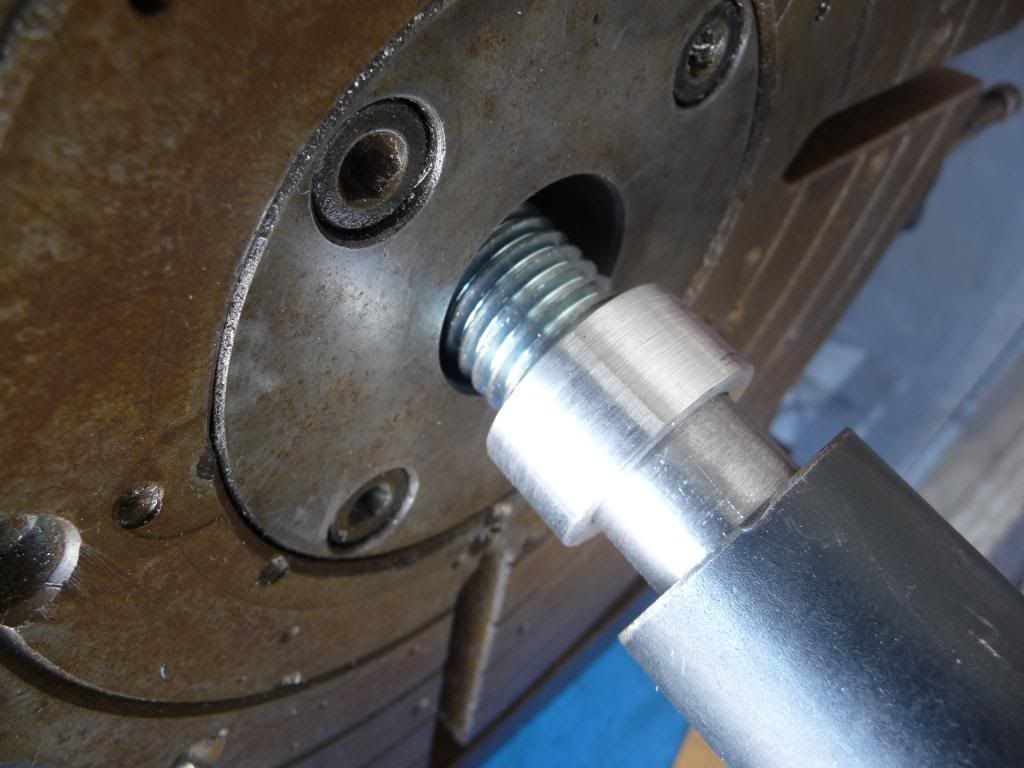 Looks like it is sturdy enough......  Run out is pretty good....about +- .001 at the base and +-.006 near the cup holes...may have to check that out further..... 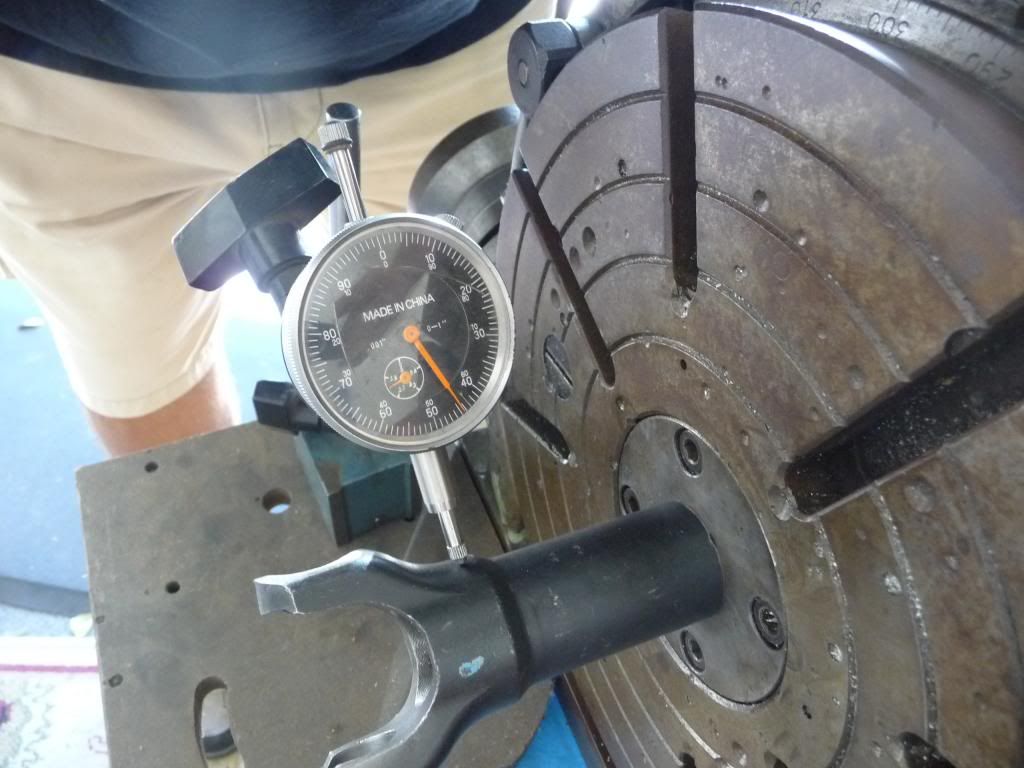 Interestingly enough, the bore and spline i.d. of the short section of the joint is considerably smaller than the longer section.....ex. ....about 1.022 for the long part of the joint and .984 (bore id not spline id) That says I will probably need to round up another big ass bolt and machine for the smaller portion of the yoke and not molest the bolt for the bigger portion.......not sure why other than to preserve the first bolt dimensions.... Next is to select an appropriate grinding wheel, it looks like only a small amount needs to be ground to establish a flat for the c rings and and the internal dimension needed to install the c ring on the cups.
|
|
|
Logged
|
|
|
|
pancho
|
 |
« Reply #7 on: October 05, 2013, 08:03:02 AM » |
|
"Run out is pretty good....about +- .001 at the base and +-.006 near the cup holes...may have to check that out further....." Not sure about your rotary table, I think mine has a Morse Taper 2 hole in the center. Would something like this cut to size help give you better alignment? http://www.ebay.com/itm/MT2-1-2-Inch-Round-Collet-/350877021679?pt=BI_Tool_Work_Holding&hash=item51b1e675ef
|
|
|
Logged
|
The most expensive things you will purchase, are those things you would not have needed if you had listened and obeyed.
|
|
|
Rio Wil
|
 |
« Reply #8 on: October 05, 2013, 07:00:56 PM » |
|
The runout at the base of the yoke is fine.....the .006 at the yoke ears might be due to not being tightened down yet....I just threw it on the table turned the nut and took a preliminary measurement. This part appears to be forged and not turned so the outside dimensions are suspect......have to check the inside dimensions around the cup area for actual runout. Having never done this before, I am not sure how much misalignment is tolerable before it translates to either vibration or undue wear on the bearing cups.....so will try to keep it to a minimum with out getting anal........  At highway speed this thing is turning some 2000-2500 rpm, so it needs to be fairly well aligned.balanced..... I think I have a coffee can of collets around here somewhere but it seems they were a shorter collet than seen in your link. The hole in the table is 1.250 on the surface and 1.100 on the back side over a 2.500 inch long bore....Not sure what MT that describes......my Bridgeport is R8, but don't know about the table.....all in all, it should be an interesting project.
|
|
|
Logged
|
|
|
|
pancho
|
 |
« Reply #9 on: October 06, 2013, 10:30:15 AM » |
|
That be a MT4 taper in your table,, what is that, a twelve inch table?? must be fun to move around. Mine is an eight inch and weighs 62lbs or so...
It certainly is an interesting project, keep the info and pictures coming.
|
|
|
Logged
|
The most expensive things you will purchase, are those things you would not have needed if you had listened and obeyed.
|
|
|
Rio Wil
|
 |
« Reply #10 on: October 06, 2013, 05:44:56 PM » |
|
|
|
|
Logged
|
|
|
|
pancho
|
 |
« Reply #11 on: October 06, 2013, 08:04:39 PM » |
|
Well, while universal joints are precision products, I believe they are mass produced, not individually hand constructed..... so I would not think that the marks are some complicated individual balancing code,,, the offset of some of the relief machining steps you measured seems to indicate that PERFECT balancing may not be as critical as one might think...??? I tried to do a bit of research on u joint manufacturing and did not come up with anything pertinent. I guess I would chalk them up as manufacturing marks and move on. If I read you right, the minor and major of the splines are centered in the forging within .001 ??
|
|
|
Logged
|
The most expensive things you will purchase, are those things you would not have needed if you had listened and obeyed.
|
|
|
Rio Wil
|
 |
« Reply #12 on: October 07, 2013, 08:20:44 AM » |
|
Correct, it seems the bore for the splines was cut on center, the splines then cut/broached, then the bore was enlarged possibly for clearance for the drive shaft, but the set up was rough and the bore was offset cut.....curious. One would think the little punch marks would be symmetrical if they were tool marks and not triangular, crescent or random in shape...... Anyway, on to looking at how to cut.grind the flats on the inner side of the ears and maintain the correct dimension for installing the clip. I was looking at a BMW site that talked about keeping the joint installed to within .002-.003 of the center of rotation for the yoke to keep vibration down.....or if too far off center it can cause "launch lurch" .... 
|
|
|
Logged
|
|
|
|
Rio Wil
|
 |
« Reply #13 on: October 07, 2013, 01:34:08 PM » |
|
Well.....appears the joke is really on me.....I just measured the cup diameters of the Precision Universal 392 ujoint and they are .002 smaller than than the original. Needless to say, that is about the amount of the press fit so these cups just slide right through. So, now back to the research, I thought the research had been done and the 392 joint was a fit but with the loose cups, it simply will not work, I am sure I did not ream the ears oversize because the old cups are still a nice tight press fit.... So I have to ask the question....has anyone any knowledge of a 392 joint being actually installed and did the cups fit with a proper press fit. The joint I bought comes in a box labeled Precision Universal, the joint is actually made by GMB in Japan.....this statement is simply a point of reference. I found the below dimensions while searching for info and they are very misleading and not to be relied on either.........so crap...... ==================================================================== outside to outside of c-clips is 1.62" three days from purchase to my front door $20.00 each free shipping! cooldude cap dia. 0.79 , overall cap to cap outside 2.337"= ==================================================================== SO IF ANYONE IS USING ONE OF THE REBUILT UNIVERSALS WITH OUT THE CUPS BEING PRESS FIT AND ONLY RETAINED BY THE CCLIPS.......REMOVE IT IMMEDIATELY OR YOU WILL DIE!!!!!!!!!! Also take a look at the picture of the 392 compared to the original.....it ain't as beefy!!!!!!! 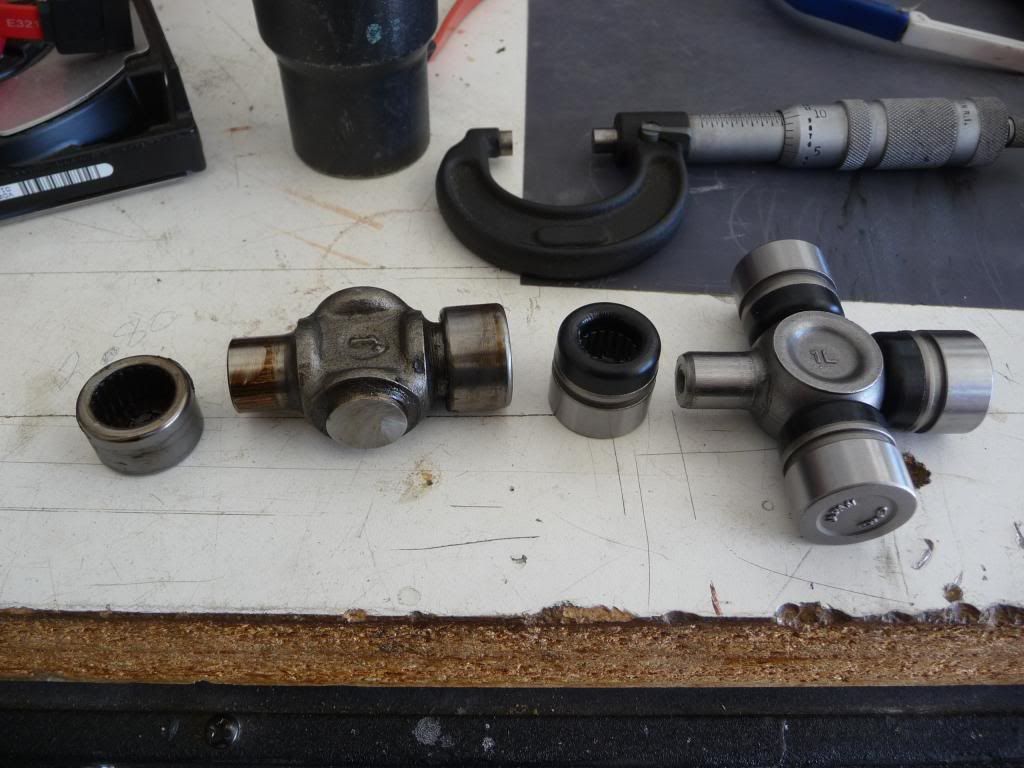
|
|
|
Logged
|
|
|
|
Rio Wil
|
 |
« Reply #14 on: October 07, 2013, 05:07:24 PM » |
|
WELL-WELL-WELL........I think I am beginning to understand. It appears the original ujoint bearing cups are what is known as "drawn cup needle bearings", these cups have a thin wall sheet metal housing. They are designed for high loads and are of good quality. The dimension of the bearing is oversize for the bore it is to live in and is intentionally shrunk upon installation to fit. The bore it fits into is dimensionally the same as a ground cup bearing (in our case .788) with a shrink fit of .790........thus a .002 interference fit. A standard ground cup bearing will essentially pass right through the ear bore of .788 because it is .788 also....thus no interference fit. I suspect this is the reason the rebuilder in Redding had such a hard time finding "good" yokes, ground bearing cups simply passed through with no interference. So the challenge then is to find a ujoint of proper dimensions with drawn cup needle bearings and they will fit our yokes just fine.....will have a nice interference fit and life is good. So the question is, where do we get such a joint.........buy it from the same vendor Honda does if that can be identified, or buy a ujoint from Honda, remove the joint and bearings and install in our good yoke......or....ya ready......just use the part from Honda and be done with it...... So....it looks like I am done with this project unless we can identify a source of the proper ujoint with bearings ..... AND to think I cratered a reasonably good ujoint to find this out.....crap  Chris mentions below that Honda CRV might have the identical ujoint...might be worth checking out. I will post this in the other thread and unless the CRV thing pans out......I'm done....
|
|
|
Logged
|
|
|
|
Rio Wil
|
 |
« Reply #15 on: October 07, 2013, 06:52:11 PM » |
|
Hmmmmm....found some ujoints at Rockford Driveline that have a bearing diameter of .791.....just what we need.....might have to check that out for the other dimensions.
|
|
|
Logged
|
|
|
|
pancho
|
 |
« Reply #16 on: October 07, 2013, 08:57:18 PM » |
|
Well now, that's certainly a fly in the ointment!!! OK,,, I see you already found this, http://rockforddriveline.com/ujointinside.htm
|
|
« Last Edit: October 07, 2013, 09:35:45 PM by pancho »
|
Logged
|
The most expensive things you will purchase, are those things you would not have needed if you had listened and obeyed.
|
|
|
|
Ricky-D
|
 |
« Reply #18 on: October 10, 2013, 03:33:29 AM » |
|
Locktite makes, along with all the thread locker,
A spline locker that's supposed to take up spaces
and remove slop.
It's high pressure and works that way you would need.
***
|
|
|
Logged
|
2000_Valkyrie_Interstate
|
|
|
pancho
|
 |
« Reply #19 on: October 11, 2013, 07:43:42 PM » |
|
I am not understanding what dimension you are finding to be the problem Rio? (I don't have a Valkyrie ujoint handy to measure), is it the inside spacing between the ears on the yokes?
|
|
|
Logged
|
The most expensive things you will purchase, are those things you would not have needed if you had listened and obeyed.
|
|
|
Rio Wil
|
 |
« Reply #20 on: October 11, 2013, 08:34:20 PM » |
|
There are a couple of dimension issues. The first is the stock ujoint has bearing cups that are .791 o.d., the bores in the ears are .788-.789.......this is a good press fit and then staked for good measure. The replacement ujoint (Precision Universal #392) has bearing cup o.d. of .788.....as stated the yoke ears are .788-.789.....this is a slip fit and this means the bearing caps are retained in the bores only with the c-clips and are free to wobble around minutely, much the same as a bad-loose bearing cup......not good. There is another ujoint available from Rockford Driveline (430-9A/B) that has the bearing cup o.d. we want of .791 which will be a nice press fit....same as factory. However the inside dimension is too small to install the c-clip and have it rest up against the inner side of the yoke. This will allow the joint to wander off center and begin to wobble. The solution to this problem was to tack weld the bearing cups in the yoke bore.......which has its own problems, ie, heating the lube in the cup. The other issue with this is the ujoint is way undersize compared to the factory unit. It's beginning to look like the best fix is to obtain the original ujoint from the Honda vendor that made the yokes/joints for Honda.....good luck with that. Also since Honda has gone to a new vendor, the ujoint in the new version might not even be the same as the original one. If anyone has one of the new u-joints, I wonder of the yoke bore and cup o.d. could be measured some way???? Ricky.....see the above comments as to why I don't think anything but a good press fit is the best solution.......other than of course......just buy a new ujoint from Honda...  I would like to pursue this just for grins to see if this exercise can be done and achieve at least factory specs......
|
|
|
Logged
|
|
|
|
pancho
|
 |
« Reply #21 on: October 12, 2013, 07:15:13 AM » |
|
The 430-9a requires a spacing of 1.315, and the 430-9b requires 1.335 to use the clips... what is the spacing between the ears?? Remember that you do not need zero clearance for the clips as the cups at .791 are a tight fit with negative clearance and will not be moving around.
|
|
|
Logged
|
The most expensive things you will purchase, are those things you would not have needed if you had listened and obeyed.
|
|
|
Rio Wil
|
 |
« Reply #22 on: October 12, 2013, 07:27:51 AM » |
|
With both of those ujoints the c-clip will be just hanging out in thin air and not anywhere close to the inside of the ear. Also the inside of the ears is not flat, so a flat surface needs to be cut to allow a reasonable c-clip fit. The inside dimension (or lockup) would need to be in the area of 1.450 to 1.490....... Both of these joints are well short of that.
These are indeed press fit but take a good look at the amount of metal around the ears that surrounds the bearing cap.....not a hell of a lot, so I want a press fit and c-clip (or staked) as original.
|
|
|
Logged
|
|
|
|
gordonv
Member
    
Posts: 5763
VRCC # 31419
Richmond BC
|
 |
« Reply #23 on: October 12, 2013, 01:42:20 PM » |
|
Could the yoke not be reamed/drilled/lathed out to the next larger size u-joint?
|
|
|
Logged
|
1999 Black with custom paint IS 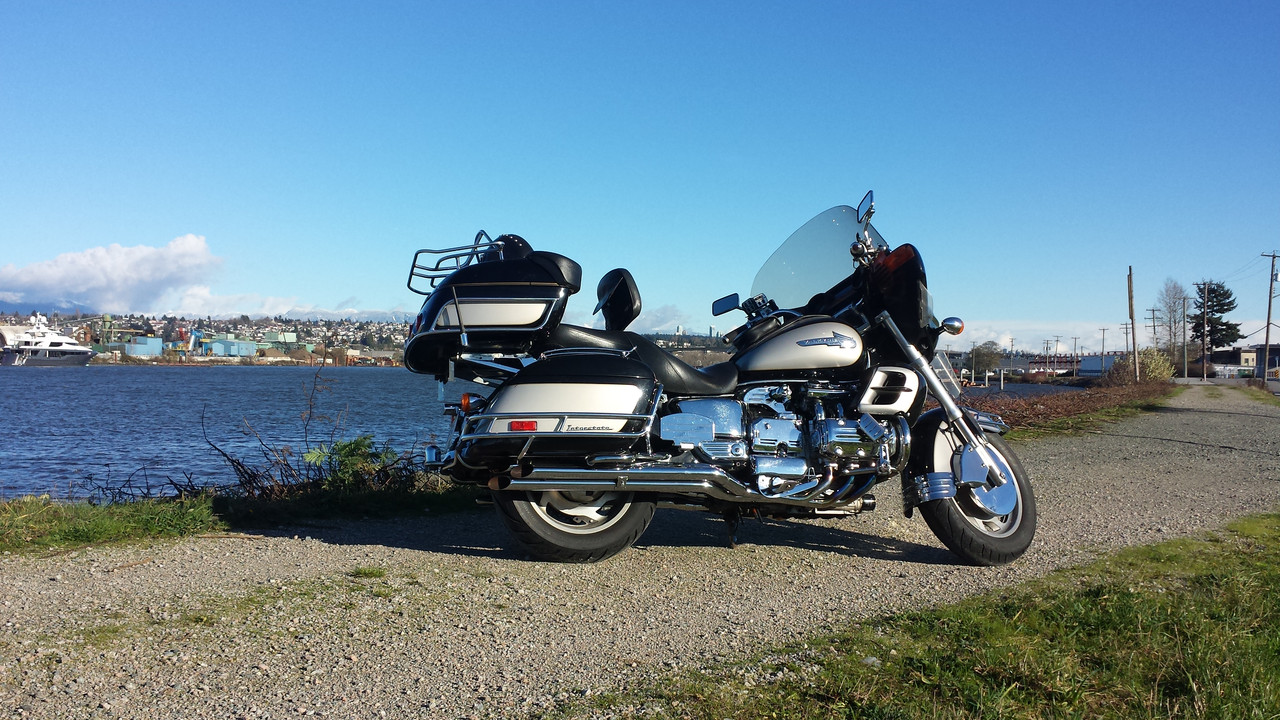 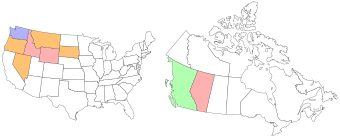
|
|
|
Rio Wil
|
 |
« Reply #24 on: October 12, 2013, 09:22:47 PM » |
|
It looks like the nest larger size is about .076 larger.....that's .038 per side, not much meat left in the ear after doing that........
|
|
|
Logged
|
|
|
|
pancho
|
 |
« Reply #25 on: October 13, 2013, 05:00:10 AM » |
|
Well, you could always use the 430-9b and build some custom clips if you don't like the gap in there, it would take a bit or research to figure the proper heat treatment to keep the clips springy,, I wonder if there is enough ear material there to stake them in and leave the clips out if you used the 430-9b?? or build up the inside of the yokes ears with steel before cutting and grinding them to size........
|
|
|
Logged
|
The most expensive things you will purchase, are those things you would not have needed if you had listened and obeyed.
|
|
|
Rio Wil
|
 |
« Reply #26 on: October 13, 2013, 04:47:17 PM » |
|
Holy smokes Batmen.....gimme a break. The idea is to rebuild an original Valk ujoint with a minimumm of effort, minimum engineering expense, minimum machining time and expense and produce a more rugged ujoint. I don't want to mine the ore, build a smelter, coke my own coke, forge my own yoke...balh blah blah...... All I want is a beefy ujoint with a .791 bearing cup, with a grease zerk (even this is optional). It needs to be installed with a properly fitted c-clip on the inner side of the yoke ear because it will not be staked as the original. The reason for the c-clip retention (or the staking retention) is because the side walls of the drawn bearing cups (ie, sheet metal) are not as thick as a typical ground bearing cup and a press fit is not sufficient. The 392 bearing cups result in a smaller diameter cross piece which is not desirable, the 430-9X is probably not any different because c-clip lock up distance seems to define the diameter of the cross piece...again inadequate. So there is no point in rebuilding a fairly sturdy factory ujoint with inferior ujoint products.....now if we can source the original ujoint and use our still good yokes, that would be a winner........I am sure we can figure out a good method of re-staking the yoke. So......find me a source of the original ujoint....  or, find a c-clip ujoint with about a 1.400-1.490 lockup and .791 bearing cups.... 
|
|
|
Logged
|
|
|
|
pancho
|
 |
« Reply #27 on: October 13, 2013, 08:38:16 PM » |
|
Well Gee Whiz Robin, when I saw you posting pictures dragging out your toys, I thought you were going to build something.....
|
|
« Last Edit: October 13, 2013, 08:40:33 PM by pancho »
|
Logged
|
The most expensive things you will purchase, are those things you would not have needed if you had listened and obeyed.
|
|
|
Rio Wil
|
 |
« Reply #28 on: October 14, 2013, 07:56:51 AM » |
|
|
|
|
Logged
|
|
|
|
Jeff K
|
 |
« Reply #29 on: October 14, 2013, 08:17:10 AM » |
|
Well.....appears the joke is really on me.....I just measured the cup diameters of the Precision Universal 392 ujoint and they are .002 smaller than than the original. Needless to say, that is about the amount of the press fit so these cups just slide right through. So, now back to the research, I thought the research had been done and the 392 joint was a fit but with the loose cups, it simply will not work, I am sure I did not ream the ears oversize because the old cups are still a nice tight press fit.... So I have to ask the question....has anyone any knowledge of a 392 joint being actually installed and did the cups fit with a proper press fit. The joint I bought comes in a box labeled Precision Universal, the joint is actually made by GMB in Japan.....this statement is simply a point of reference. I found the below dimensions while searching for info and they are very misleading and not to be relied on either.........so crap...... ==================================================================== outside to outside of c-clips is 1.62" three days from purchase to my front door $20.00 each free shipping! cooldude cap dia. 0.79 , overall cap to cap outside 2.337"= ==================================================================== SO IF ANYONE IS USING ONE OF THE REBUILT UNIVERSALS WITH OUT THE CUPS BEING PRESS FIT AND ONLY RETAINED BY THE CCLIPS.......REMOVE IT IMMEDIATELY OR YOU WILL DIE!!!!!!!!!! Also take a look at the picture of the 392 compared to the original.....it ain't as beefy!!!!!!! 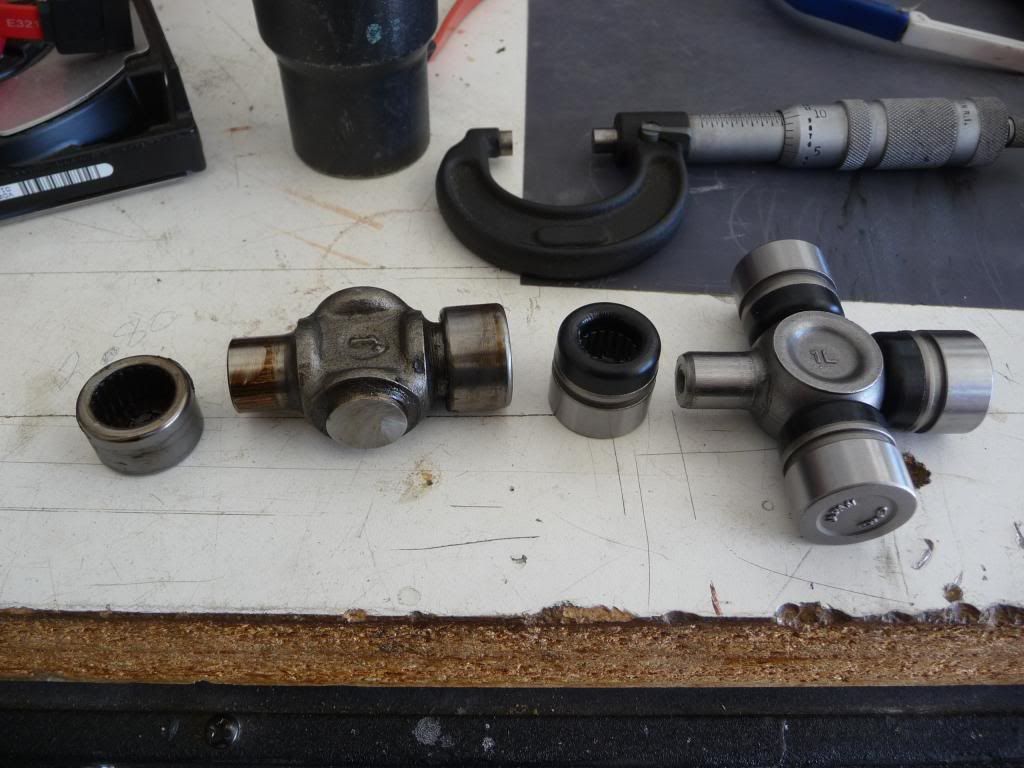 Been there, done that. It shattered on the way to IZ many many many years ago.
|
|
|
Logged
|
|
|
|
Rio Wil
|
 |
« Reply #30 on: October 21, 2013, 08:56:20 PM » |
|
Hmmmmm... I might have found a suitable ujoint in England (IMS number GUN45). It is cap to cap of 2.078 and a cup diameter of .790......a reasonable press fit. It would also allow for being restaked . Have contacted IMS for quote plus shipping and customs? Don'ty know yet if it is a drawn sheet metal cup or a ground steel cup, The drawn sheet metal cup has thinner walls and allows for a larger diameter bearing post on the joint.....
|
|
|
Logged
|
|
|
|
Rio Wil
|
 |
« Reply #31 on: October 22, 2013, 06:09:56 PM » |
|
|
|
|
Logged
|
|
|
|
Rio Wil
|
 |
« Reply #32 on: October 29, 2013, 05:02:06 PM » |
|
Got a lead on a ujoint in the UK from IMS that appears to have the exact dimensions of the original ujoint cross piece. They could supply the part at $26 plus $48 shipping so I asked for a distributor in the US. Luckily there was on in southern CA. They had the part at $26 and UPS shipping was $15. The part is made by GMB in Japan and although it does not have a grease zert, it is of the drawn cup design and does have the larger arms like the original compared to the 392 part. Cup diameter is .790 which gives a nice press fit and it is a staked part like the original. Drawn cups are not sturdy enough to just rely on a press fit. So I will soon install the part in the yokes, figure a way to do the staking and centering the cross piece for runout and see how this goes. Hopefully I can recover what was a reasonable good ujoint I destroyed for this experiment and maybe even be better since it has a new cross piece of proper dimensions. This joint is used in a variety of ATV's. Dick.....I wonder if your guy in Redding might have renewed interest in doing this since it is considerably simpler than having to machine flats for c-rings. Just remove the stakes, press out the old cross piece, press in the new cross piece, center and re-stake...... I figure the yokes are good for one maybe two re-stakings if done carefully. 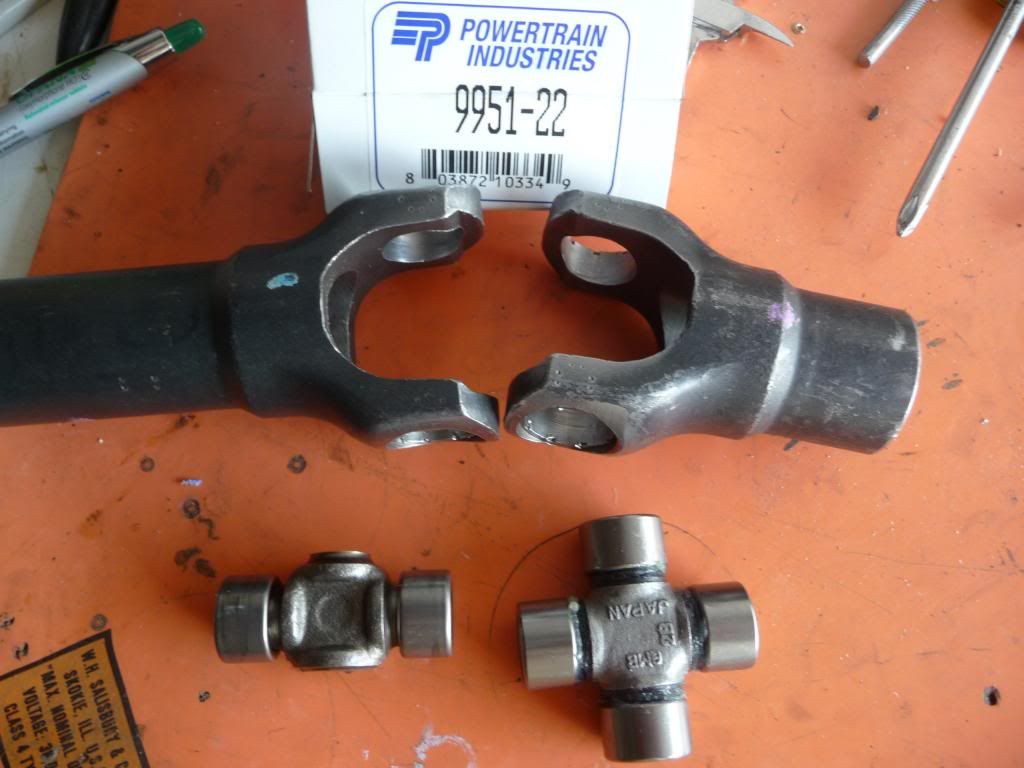
|
|
|
Logged
|
|
|
|
Rio Wil
|
 |
« Reply #33 on: October 31, 2013, 11:33:00 AM » |
|
AT THIS POINT I AM PUTTING THIS PROJECT ON A EXTENDED HOLD DUE TO THE NEW UJOINT NOT BEING AS A GOOD A FIT AS I FIRST THOUGHT.
THIS PROJECT DATA SHOULD NOT NOT.....REPEAT NOT BE USED BY ANONE IN AN ATTEMPT TO USE THE PARTS MENTIONED TO REBUILD A JOINT AND INSTALL IT IN THEIR MOTORCYCLE.
IF YOU NEED A UJOINT, I WOULD RECOMMEND BUYING A NEW ONE FROM HONDA...OR OTHER PARTS SUPPLIER.
|
|
|
Logged
|
|
|
|
The emperor has no clothes
|
 |
« Reply #34 on: October 31, 2013, 02:05:44 PM » |
|
AT THIS POINT I AM PUTTING THIS PROJECT ON A EXTENDED HOLD DUE TO THE NEW UJOINT NOT BEING AS A GOOD A FIT AS I FIRST THOUGHT.
THIS PROJECT DATA SHOULD NOT NOT.....REPEAT NOT BE USED BY ANONE IN AN ATTEMPT TO USE THE PARTS MENTIONED TO REBUILD A JOINT AND INSTALL IT IN THEIR MOTORCYCLE.
IF YOU NEED A UJOINT, I WOULD RECOMMEND BUYING A NEW ONE FROM HONDA...OR OTHER PARTS SUPPLIER.
Dang I thought you were just about to make a breakthrough. I enjoyed following your progress even though it was over my head.
|
|
|
Logged
|
|
|
|
Rio Wil
|
 |
« Reply #35 on: October 31, 2013, 04:30:43 PM » |
|
|
|
|
Logged
|
|
|
|
Ricky-D
|
 |
« Reply #36 on: November 01, 2013, 10:17:21 AM » |
|
Yeah, good effort, but I feel it's futile.
***
|
|
|
Logged
|
2000_Valkyrie_Interstate
|
|
|
Rio Wil
|
 |
« Reply #37 on: November 01, 2013, 09:32:48 PM » |
|
Yeah.....sure would like to know who makes the cross piece for Honda......must be a custom size.
|
|
|
Logged
|
|
|
|
Jeff K
|
 |
« Reply #38 on: November 04, 2013, 10:19:03 AM » |
|
I've been down this road once, but it was years ago. I was hoping things had changed but it appears not.
|
|
|
Logged
|
|
|
|
Rio Wil
|
 |
« Reply #39 on: November 04, 2013, 04:50:42 PM » |
|
One would think with the thousands of ujoints out there, it would be easy to find a suitable replacement. There is a cross piece with a .791 cup which is ideal, but the lock up is only some 1.330 and it would require a spacer to go with the c-clip.....not desirable and I suspect the cross piece is not as beefy as the original which would lead to early failure. I sure would be interested in the dimensions of the "new" u-joint Honda is having manufactured. Been a fun project but it appears I have wasted a good spare in the process.....don't know how to spell sa-la-vie..... 
|
|
|
Logged
|
|
|
|
|