hubcapsc
Member
    
Posts: 16789
upstate
South Carolina
|
 |
« on: April 01, 2016, 10:16:04 AM » |
|
I was working on the Log Truck last Friday when work spun up, now I'm in California and the Log Truck is partially assembled back in South Carolina. While moving back and forth between my laptop and the Log Truck all day on Saturday, I put the shocks back on before tightening the axle... I reached up in there and tightened the axle with an adjustable wrench, but I'm not satisfied with that... I've been thinking I'll get a 27mm box-end from Lowes when I get home and it will fit up in there and I'll get the axle nut satisfyingly tight that way... Will the 27 box-end wrench really fit up in there like I'm imagining? Here's the Log Truck for those who don't read my ramblings on the general board...  -Mike
|
|
« Last Edit: March 20, 2019, 05:47:49 AM by hubcapsc »
|
Logged
|
|
|
|
KY,Dave (AKA Misunderstood)
Member
    
Posts: 4146
Specimen #30838 DS #0233
Williamsburg, KY
|
 |
« Reply #1 on: April 01, 2016, 10:32:55 AM » |
|
I don't have a 27 mm wrench but looks like you could get the opened end on there for 1/4 turn at a time due to the shape of the swingarm. Holding a 7/8 just to see I don't think there's enough room to get the boxend on.
|
|
« Last Edit: April 01, 2016, 10:35:06 AM by KY,Dave (AKA Misunderstood) »
|
Logged
|
|
|
|
Daniel Meyer
Member
    
Posts: 5493
Author. Adventurer. Electrician.
The State of confusion.
|
 |
« Reply #2 on: April 01, 2016, 10:36:41 AM » |
|
You should loosen the 4 nuts that hold the pumpkin on to the swing-arm before tightening the axle.
I think the wrench would get in there (would on a standard anyway).
|
|
|
Logged
|
CUAgain, Daniel Meyer 
|
|
|
Bagger John - #3785
|
 |
« Reply #3 on: April 01, 2016, 10:47:12 AM » |
|
You should loosen the 4 nuts that hold the pumpkin on to the swing-arm before tightening the axle.
I think the wrench would get in there (would on a standard anyway).
This is the correct approach.
|
|
|
Logged
|
|
|
|
hubcapsc
Member
    
Posts: 16789
upstate
South Carolina
|
 |
« Reply #4 on: April 01, 2016, 10:48:26 AM » |
|
I don't have a 27 mm wrench but looks like you could get the opened end on there for 1/4 turn at a time due to the shape of the swingarm. Holding a 7/8 just to see I don't think there's enough room to get the boxend on.
Fooey... the open end will only be a little more confidence inspiring than the adjustable wrench, but it will be longer and have that feel I'm looking for... I don't use the torque wrench on the axle (maybe I should), rather I tighten it until it "feels" right... I don't need to make it harder than it is... I could just take the shocks back off and use the 27mm socket  ... -Mike
|
|
|
Logged
|
|
|
|
KY,Dave (AKA Misunderstood)
Member
    
Posts: 4146
Specimen #30838 DS #0233
Williamsburg, KY
|
 |
« Reply #5 on: April 01, 2016, 10:50:07 AM » |
|
I don't have a 27 mm wrench but looks like you could get the opened end on there for 1/4 turn at a time due to the shape of the swingarm. Holding a 7/8 just to see I don't think there's enough room to get the boxend on.
Fooey... the open end will only be a little more confidence inspiring than the adjustable wrench, but it will be longer and have that feel I'm looking for... I don't use the torque wrench on the axle (maybe I should), rather I tighten it until it "feels" right... I don't need to make it harder than it is... I could just take the shocks back off and use the 27mm socket  ... -Mike Would be worth the peace of mind to do it right
|
|
|
Logged
|
|
|
|
hubcapsc
Member
    
Posts: 16789
upstate
South Carolina
|
 |
« Reply #6 on: April 01, 2016, 10:54:58 AM » |
|
You should loosen the 4 nuts that hold the pumpkin on to the swing-arm before tightening the axle.They're still loose...  (I put in a new u-joint)... I think the wrench would get in there (would on a standard anyway).I hope you're right... I'd like to just bolt the last few things back on and go for a test ride Sunday afternoon after being out here all week... the bags are still off, so it's a standard right now  ... BTW: I reused the old u-joint boot and used Lady Draco's "unroll it" method to get it back on to the swingarm... it was only a tiny bit frustrating... BTW-2: Hang in there Daniel on the storms and stuff... -Mike
|
|
|
Logged
|
|
|
|
Patrick
Member
    
Posts: 15433
VRCC 4474
Largo Florida
|
 |
« Reply #7 on: April 01, 2016, 11:14:53 AM » |
|
I really don't often use a torque on that axle fastener either. If I remember correctly that spec is 80#. I usually end up around the 70# range which is plenty. That nut is not going anywhere, it'll stay put.
|
|
|
Logged
|
|
|
|
The emperor has no clothes
|
 |
« Reply #8 on: April 01, 2016, 11:49:45 AM » |
|
Interesting..... The front and rear axles are the only thing I use a torque wrench on. 
|
|
|
Logged
|
|
|
|
indybobm
|
 |
« Reply #9 on: April 01, 2016, 11:50:26 AM » |
|
Maybe you could remove the nuts holding the rear of the exhaust on and pull the exhaust away enough to get the box wrench in there.
|
|
|
Logged
|
So many roads, so little time VRCC # 5258
|
|
|
hubcapsc
Member
    
Posts: 16789
upstate
South Carolina
|
 |
« Reply #10 on: April 01, 2016, 11:52:40 AM » |
|
Maybe you could remove the nuts holding the rear of the exhaust on and pull the exhaust away enough to get the box wrench in there.
the only thing that might be in the way is the shape, or profile, of the swingarm where the axlenut seats in... that's why an open-end might get in there and a box-end might not... -Mike "I think..."
|
|
|
Logged
|
|
|
|
Chrisj CMA
|
 |
« Reply #11 on: April 01, 2016, 11:54:08 AM » |
|
OK, two things. And I just read Patrick's post about old men, so I don't really care what anyone else thinks, I have been doing rear wheels on eight or so Valkyries for years and I know Im right.
1. The Torque setting on the axel is 81, that is high but its for a reason and its not just so it don't come loose. There is a solid torque line of steel from the nut to the head of the axle. These parts, spacers and bearings need to act like a solid bar of steel to maintain integrity for the drive system, and achieve alignment of the final drive. So don't scrimp its only takes a second or two more to make sure its right.
2. The axle should be torqued BEFORE tightening the 4 final drive bolts and BEFORE attaching the right side shock so nothing is impeding the mating of the wheel and final drive, that is how alignment is achieved. That's why I hate when people say you should torque four final drive to swing arm nuts last. Not last, right after the axle nut and right before attaching the right side shock.
OK, off my soapbox. Just do it right, final drives are getting harder to find!
|
|
« Last Edit: April 01, 2016, 12:05:11 PM by Chrisj CMA »
|
Logged
|
|
|
|
KY,Dave (AKA Misunderstood)
Member
    
Posts: 4146
Specimen #30838 DS #0233
Williamsburg, KY
|
 |
« Reply #12 on: April 01, 2016, 12:41:49 PM » |
|
Maybe you could remove the nuts holding the rear of the exhaust on and pull the exhaust away enough to get the box wrench in there.
the only thing that might be in the way is the shape, or profile, of the swingarm where the axlenut seats in... that's why an open-end might get in there and a box-end might not... -Mike "I think..." It's the exhaust that kept me from getting the boxend on when I looked for you.
|
|
|
Logged
|
|
|
|
Chrisj CMA
|
 |
« Reply #13 on: April 01, 2016, 02:32:55 PM » |
|
You should loosen the 4 nuts that hold the pumpkin on to the swing-arm before tightening the axle.They're still loose...  (I put in a new u-joint)... I think the wrench would get in there (would on a standard anyway).I hope you're right... I'd like to just bolt the last few things back on and go for a test ride Sunday afternoon after being out here all week... the bags are still off, so it's a standard right now  ... BTW: I reused the old u-joint boot and used Lady Draco's "unroll it" method to get it back on to the swingarm... it was only a tiny bit frustrating... BTW-2: Hang in there Daniel on the storms and stuff... -Mike Mike, it won't even take 15 minutes to remove the shocks, attach your turn buckle thinggy, torque the axle, then torque the four bolts and then replace the shocks
|
|
|
Logged
|
|
|
|
hubcapsc
Member
    
Posts: 16789
upstate
South Carolina
|
 |
« Reply #14 on: April 01, 2016, 02:46:18 PM » |
|
Mike, it won't even take 15 minutes to remove the shocks, attach your turn buckle thinggy, torque the axle, then torque the four bolts and then replace the shocks
Yeah, it seemed like a drag on hectic Saturday when I had to give up putting the bike back together, but it won't be nothing but a thang this Sunday when I'll have eight sunny hours after Church to tighten the axle properly and ride around on some neighborhood roads to test it out...
The work interference resulted in the successful completion of a risky three year project, but I wish I had had all day to work on the bike like I thought I would... I didn't get a chance to do the "vise test" on the new u-joint so that I could feel the difference between it and the old one... two of us felt the tiny looseness in the old one, though, so I'm confident it was worth replacing...
-Mike
|
|
|
Logged
|
|
|
|
pancho
|
 |
« Reply #15 on: April 01, 2016, 03:16:18 PM » |
|
Mike,, you reused old u-joint?? I thought you determined there was some play in it when you put it into your neighbors vice..?? Chris got it nailed on the reasons why the axle should be torqued properly, rigidity of all the associated parts . There is a lot of torque being applied on that plane as the final changes the direction of rotation, especially under hard acceleration. I have two torque wrenches, different ranges of sweet spot, and use them a lot on the Valk.
|
|
|
Logged
|
The most expensive things you will purchase, are those things you would not have needed if you had listened and obeyed.
|
|
|
hubcapsc
Member
    
Posts: 16789
upstate
South Carolina
|
 |
« Reply #16 on: April 01, 2016, 03:37:51 PM » |
|
Mike,, you reused old u-joint?? I thought you determined there was some play in it when you put it into your neighbors vice..?? Chris got it nailed on the reasons why the axle should be torqued properly, rigidity of all the associated parts . There is a lot of torque being applied on that plane as the final changes the direction of rotation, especially under hard acceleration. I have two torque wrenches, different ranges of sweet spot, and use them a lot on the Valk.
No, I put the new u-joint in, I just didn't take the time to do the "vise test" on it so that I could feel the difference between it and the old one that we (me and neighbor Dan) agreed had some slack in it. I have a beam torque wrench that I should use on the axle, but I usually just tighten it... I hope I report Sunday night that I took the shocks off, torqued the axle, tightened the four nuts, replaced the shocks, bolted all the other stuff back on and took a good ride  -Mike
|
|
|
Logged
|
|
|
|
Red Diamond
|
 |
« Reply #17 on: April 03, 2016, 06:21:47 PM » |
|
If you torque by feel, you can use an 1 1/16" open end on that nut. Should you choose to use a torque wrench, you can still use the same size in a crows foot type open end. Don't forget the Allen backup.
|
|
|
Logged
|
 If you are riding and it is a must that you keep your eyes on the road, you are riding too fast.
|
|
|
hubcapsc
Member
    
Posts: 16789
upstate
South Carolina
|
 |
« Reply #18 on: April 03, 2016, 07:03:31 PM » |
|
It just took a second to take the shocks off and check the torque on the axle nut, tighten the four nuts and put the shocks back on... I had done OK on the torque with the crescent wrench  ... It took a little longer to remember how this went back together, I had plenty of room last Saturday to unroll the old u-joint boot back on, though:  Then on to fixing my leaky shift seal...  Got the mess cleaned up some, I'll have to go after again with some degreaser and a brush...  I followed Daniel Meyer's instructions, the package says "4 X 03" now, so I guess that's not a cross-reference number... http://lifeisaroad.com/valkshiftseal.html50 (s)miles later it was still leak free...  I took pictures of my other stuff last week as I cleaned it up and put it back together... my flange and drive splines aren't any worse than they were last year...    I guess I forgot to take one of the cup, so much for record keeping... I went for an awesome test ride, I guess I'll post those pictures on the general board... -Mike
|
|
|
Logged
|
|
|
|
0leman
|
 |
« Reply #19 on: April 04, 2016, 08:18:51 AM » |
|
I have been using a 1 1/16" box in wrench to tighten/loosen the axle nut since 2008. I have almost 70k miles that I have put on (100k on the clock). that's 7 times taking off the axle and replacing it. No problems reaching the nut sitting on the floor behind her.
|
|
|
Logged
|
2006 Shadow Spirit 1100 gone but not forgotten 1999 Valkryie I/S Green/Silver
|
|
|
Gryphon Rider
Member
    
Posts: 5227
2000 Tourer
Calgary, Alberta
|
 |
« Reply #20 on: April 04, 2016, 10:39:41 AM » |
|
I followed Daniel Meyer's instructions, the package says "4 X 03" now, so I guess that's not a cross-reference number...  I am pretty sure that is a manufacturing lot number, and has nothing to do with the size. Most other Honda parts have a similar number, and if you look at photos of otherwise identical parts, that number will change while the part number stays the same.
|
|
|
Logged
|
|
|
|
da prez
|
 |
« Reply #21 on: April 06, 2016, 05:27:26 AM » |
|
My turn on the soap box. When torquing , it takes 10% more to move a nut or bolt. So if you torque to 75 fp, and then go to 80 , there is no increase in torque. The wrench will click , but no increase. This was learned and proven in a tech school many years ago. Torque to 65 or so and then to 81. I do it this way without problems . I know there will be some doubters , but it is like the greased pig theory , pretty soon , you realize that the pig enjoys the fight.
da.prez
|
|
|
Logged
|
|
|
|
hubcapsc
Member
    
Posts: 16789
upstate
South Carolina
|
 |
« Reply #22 on: April 06, 2016, 05:36:49 AM » |
|
My turn on the soap box. When torquing , it takes 10% more to move a nut or bolt. So if you torque to 75 fp, and then go to 80 , there is no increase in torque. The wrench will click , but no increase. This was learned and proven in a tech school many years ago. Torque to 65 or so and then to 81. I do it this way without problems . I know there will be some doubters , but it is like the greased pig theory , pretty soon , you realize that the pig enjoys the fight.
da.prez
If my beam wrench clicks, something broke!  -Mike
|
|
|
Logged
|
|
|
|
pancho
|
 |
« Reply #23 on: April 06, 2016, 06:57:52 AM » |
|
Did the new u-joint take care of the problem Mike?
|
|
|
Logged
|
The most expensive things you will purchase, are those things you would not have needed if you had listened and obeyed.
|
|
|
hubcapsc
Member
    
Posts: 16789
upstate
South Carolina
|
 |
« Reply #24 on: April 06, 2016, 07:27:35 AM » |
|
Did the new u-joint take care of the problem Mike?
I'll have to do some aggressive 80+mph Interstate type riding to really know... I went for a fun test ride Sunday on farm roads and rode to work on Monday, all I know is that it seems great and I know for sure that my driveline is good from one end to the other   -Mike
|
|
|
Logged
|
|
|
|
big poppa pump
|
 |
« Reply #25 on: April 06, 2016, 09:55:19 AM » |
|
My turn on the soap box. When torquing , it takes 10% more to move a nut or bolt. So if you torque to 75 fp, and then go to 80 , there is no increase in torque. The wrench will click , but no increase. This was learned and proven in a tech school many years ago. Torque to 65 or so and then to 81. I do it this way without problems . I know there will be some doubters , but it is like the greased pig theory , pretty soon , you realize that the pig enjoys the fight.
da.prez
Ross, I never knew this. However, call it luck or intuition, I've always been doing it this way, increments of 15-20 ft/lbs.
|
|
|
Logged
|
VRCC#35870 VRCCDS#0266 1998 Valkyrie Hot Rod 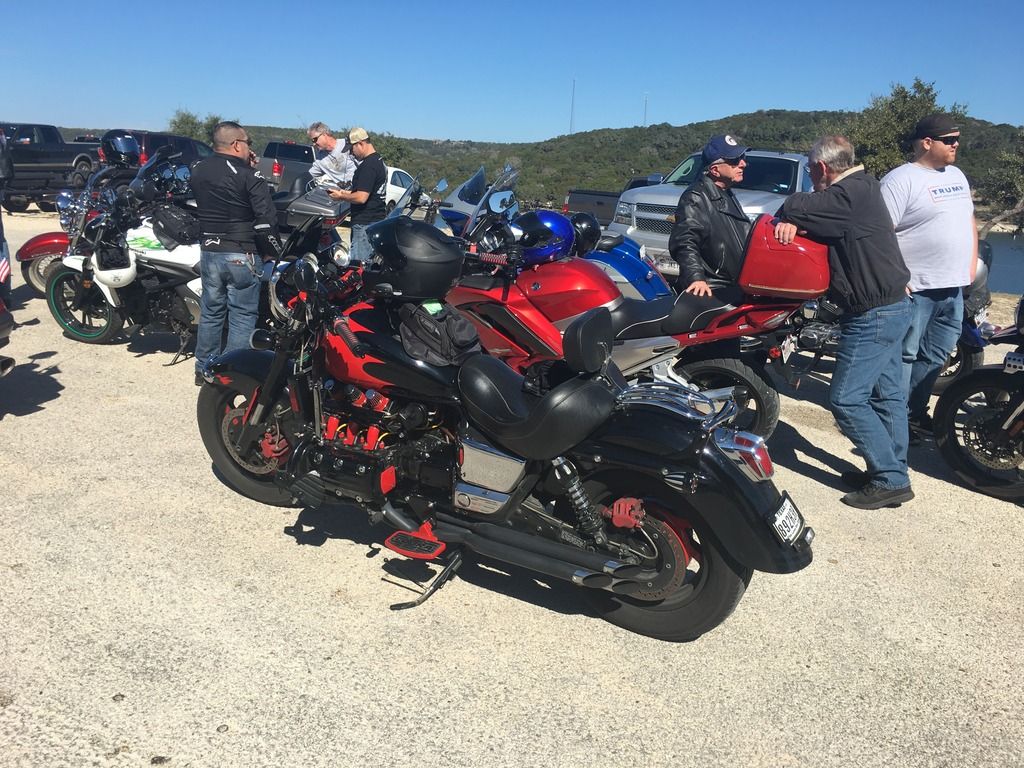
|
|
|
Patrick
Member
    
Posts: 15433
VRCC 4474
Largo Florida
|
 |
« Reply #26 on: April 06, 2016, 12:26:35 PM » |
|
I've watched folks incorrectly use torque wrenches for decades. But, there is a right and wrong way [ well, more than one] to do just about anything and that includes a torque value. Alway sneak up on the value.
|
|
|
Logged
|
|
|
|
Gryphon Rider
Member
    
Posts: 5227
2000 Tourer
Calgary, Alberta
|
 |
« Reply #27 on: April 06, 2016, 02:41:28 PM » |
|
I've watched folks incorrectly use torque wrenches for decades. But, there is a right and wrong way [ well, more than one] to do just about anything and that includes a torque value. Alway sneak up on the value.
I see no point in "sneaking up" on the specified torque of a single fastener, like an axle nut. I do see the point of having the nut turning as you reach the specified torque, rather than ending one swing of the wrench without it clicking, then having it click at the beginning of the next swing. It takes more force to overcome the initial friction from a stop than it does to keep something moving.
|
|
|
Logged
|
|
|
|
|