Here's another pic of the crack where it wraps around:
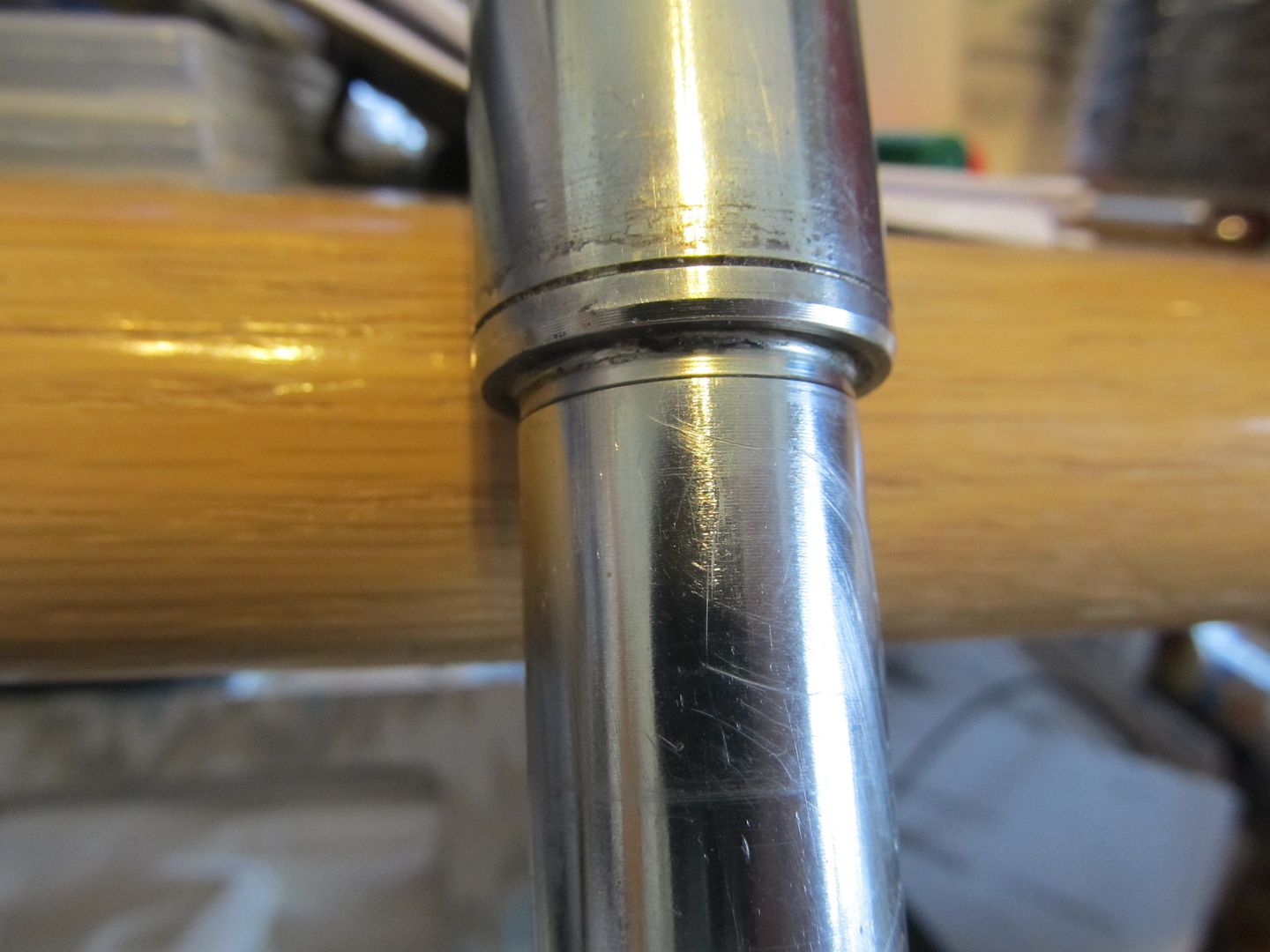
It almost hits larger diameter end, but stops about 0.10" shy. I'm going to find some dye penetrant this week to highlight this for a photo.
About the wrecked bike, don't know, but I don't think so; the bike came from a local bike shop, 36,000 miles on it. But neither the fork bottoms nor the axle ends are buggered.
Overtightening - maybe. But I would think that over-tightening the axle bolt would strip the threads before material failure. I would certainly hope this is the designed-in failure mode.
EDIT - replying to this as it was added during my post - In using one axle to punch/beat through/tap the other one out - steel should not fail under these low impacts. I's not as if I was using a 5lb sledge, swinging mightily, multiple times. Rather, a 1 lb mallet tapping from maybe 6" away, with the other axles moving 1/2"-1" each time. I generally use a 3/8" socket extension, but did not have enough lengths handy.
My theory (thought about this a lot last night) is overloading/over-stressing.
The stock VALK is about 750 lbs with a full tank of gas, at about a 50% front-rear weight distribution. With a Motorvation F2 steel frame, sidecar body, battery, air horn/compressor, tools, spares, gear for a week trip, canine, and wife, we are prolly real close to 1200-1300 lbs. Albeit spread over 3 wheels.
Combine that with:
1. A 6 degree rake to the triples in order to make the VALK steer a bit better due to the hack, and
2. A 1.5" fork extensions to make up for the height lost due to the triple tree rake, and
3. A really rough hard pack washboard and potholed 3 mile driveway, that I usually deal with by speed. I can ride it at a walking speed, taking an hour to go three miles; or at about 40-45 mph, providing a relative smooth ride, but which works because it is too fast for the forks to respond to the rough road, thereby transferring the rapid loads/unloads to the "hard parts" of the bike. Like axles and bearings.
With all the above, I think it just overloaded the hollow axle. A hollow axle is typically a good design on a motorcycle. Without getting into a "which oil is best" discussion, a hollow axle, when compared to a solid of same diameter, provides good weight savings, with little loss of strength.
BUT. It also changes the failure mode. A solid axle will bend before failure. A hollow axle cracks, as the load carrying outer diameter does not have a solid core to help absorb forces. It has almost the same load carrying ability, but has lost its toughness, for lack of a better word.
Not a good failure mode on a part that is difficult to visually inspect on a regular basis. Just what is the inspection interval on an axle???
All that said, on some machining forums I visited last night, JAP axle material is generally not highly regarded. Other materials (4130/4140, etc) are much stronger and tougher. The VALK LL's from WASP came with their own axle - I have an email to them to see what material they use, as their axle is about 2" longer than the VALK stock axle.
I'll post this over on the Sidecar.com forum, as there are some HACK manufacturers over there who have way more experience. I'll update this as I learn more.