Rusty Pipes
|
 |
« on: April 29, 2017, 03:20:58 PM » |
|
I can not get the axle nut on right side to turn. Right pinch bolts are removed, left pinch bolts still tight. Gave it all a shot of PB Blaster first thing. So far tried breaker bar with cheater pipe. 1/2" CP impact gun cranked up to 110 psi. Put the head of a 3 lb sledge against nut and cracked several times with a 32 oz ball pein. Tried impact and breaker bar again. Breaker bar had a pretty good bow to it but not bent. I filled axle with PB Blaster and on outside also. Just letting it soak now. Will try again tomorrow. I do have a 250A welder but would rather not use that till last resort. Front tire is dated 4001...Any suggestions? Thanks Folks, I'm feeling a little ill right now. 
|
|
|
Logged
|
|
|
|
Chrisj CMA
|
 |
« Reply #1 on: April 29, 2017, 03:33:01 PM » |
|
Apply some heat. Heat gun should make a big difference
|
|
|
Logged
|
|
|
|
Firefighter
|
 |
« Reply #2 on: April 29, 2017, 03:36:20 PM » |
|
If I read everything correctly I would be doing what you are doing. Make sure you have a good fitting six point socket, might heat with a heat gun and hammer with that impact. I even use the air impact forward and then reverse to try and break bolts loose. I never had that problem with the axle bolt before. Hopefully someone has a better ideal.
|
|
|
Logged
|
2000 Valkyrie Interstate, Black/Red 2006 Honda Sabre 1100 2013 Honda Spirit 750 2002 Honda Rebel 250 1978 Honda 750
|
|
|
Blackduck
|
 |
« Reply #3 on: April 29, 2017, 04:26:35 PM » |
|
If someone has used the wrong Loctite in there you will need heat to crack it. Really need a good torch to heat it quickly. If it is corrosion you may have to drill a hole in the head of the nut to get the PB into the inner threads. All the best Steve.
|
|
|
Logged
|
2001 Standard, 78 Goldwing, VRCC 21411
|
|
|
da prez
|
 |
« Reply #4 on: April 30, 2017, 08:00:25 AM » |
|
If all else fails , split the nut and replace it. Put a support (jack stand large hammer etc) under it and use a chisel to expand the nut. The nut is cheaper than the axle. Do it in a couple of places and then remove with proper socket.
da prez
|
|
|
Logged
|
|
|
|
Rusty Pipes
|
 |
« Reply #5 on: April 30, 2017, 09:24:31 AM » |
|
I looked at the parts fich. What they call a nut is actually a bolt that threads into the hollow axle. I did try the forward/backward thing with the impact. No way I'm using a torch. I may hook the welder to both ends of the axle and let it cook for a while to heat it up. Would have to be real carefull not to get too hot. Don't mind cooking seals but don't want to damage metal parts. Hmmm 
|
|
|
Logged
|
|
|
|
old2soon
|
 |
« Reply #6 on: April 30, 2017, 09:41:54 AM » |
|
Axle axle nut and the pinch bolts are all steel. The lower fork area where everything hooks up is aluminum. Reset the pinch bolts you loosened. When you get it apart and on the reinstall use anti seize on the pinch bolt threads and on the axle nut. The recess for the axle nut DO make it a tad might Interesting! Ex Navy and retired over the road trucker and my Phatt Ghurl at times has expanded my cursing vocabulary!  RIDE SAFE.
|
|
|
Logged
|
Today is the tommorow you worried about yesterday. If at first you don't succeed screw it-save it for nite check. 1964 1968 U S Navy. Two cruises off Nam. VRCCDS0240 2012 GL1800 Gold Wing Motor Trike conversion
|
|
|
da prez
|
 |
« Reply #7 on: April 30, 2017, 09:45:03 AM » |
|
Man , I totally forgot that. I do more work on HD's than Valks. I guess I should have had the brain engaged before putting the key board in gear. Just a switch of techniques , large hammer for a buffer on the fixed end and then hit the bolt end a few good raps. Try this before the heat.
da prez
|
|
|
Logged
|
|
|
|
gordonv
Member
    
Posts: 5763
VRCC # 31419
Richmond BC
|
 |
« Reply #8 on: April 30, 2017, 10:24:53 AM » |
|
Thinking here, haven't had one this tight.
You currently have the bolt/nut side pinch bolts loose? Before removing the bolt, tighten the pinch bolts again. More grip on the axle to hold it from turning.
But first, loosen both sides pinch bolt, firmly tap the axle towards the bolt, and then tighten all the pinch bolts.
My though there is that if the axle moves at all, it will lessen the force the bolt has on the fork. Meaning it's now only the threads holding it. Might be able to get in there with some penetrating oil. I have the receipt for the home made one I saved. Acetone/ATF 50/50 mix. Bought the acetone, need to find an open bottle of ATF (I'm sure its in the garage), and make some up. Will test it at work on corroded appliance feet (bolts with rubber pads), to refurbish used machines.
I would use heat, or at least get it outside on a warm day. Apply cold to the bolt before turning.
Only advantage, axles are cheap, if the bolt breaks. If that happens, then the axle can now come out.
|
|
|
Logged
|
1999 Black with custom paint IS 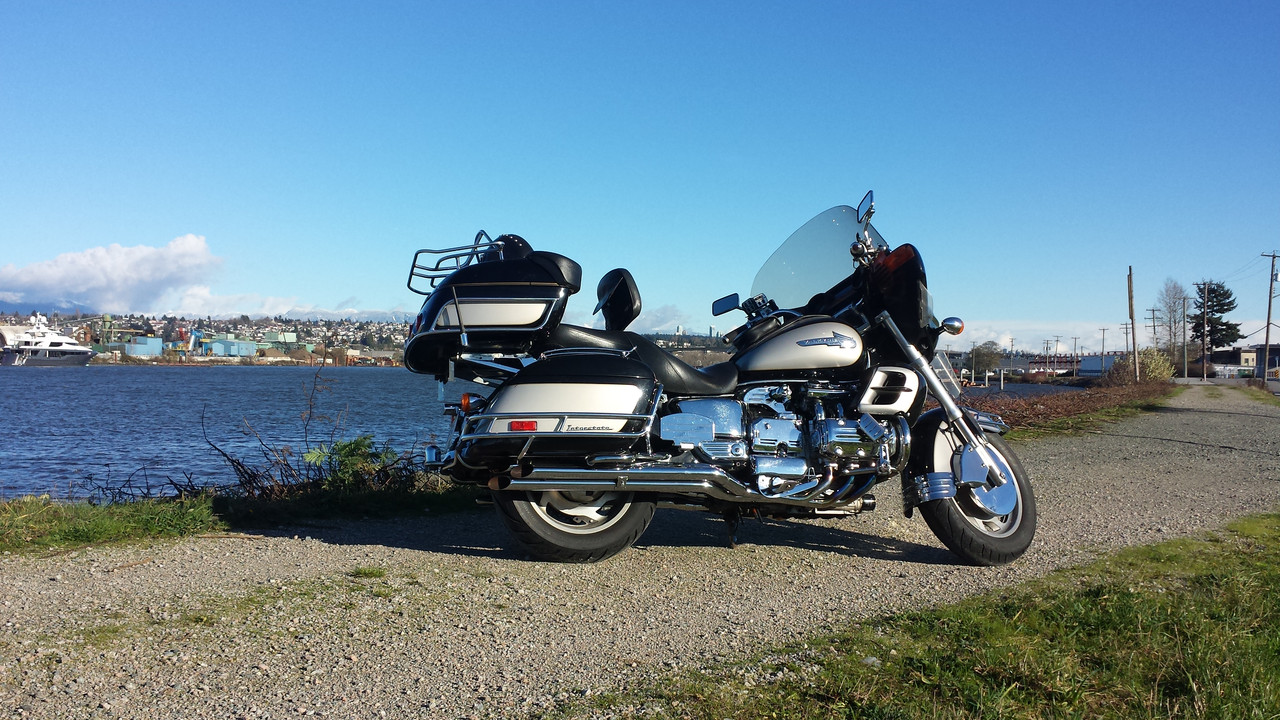 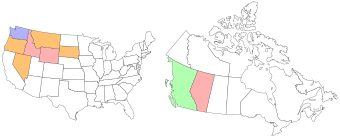
|
|
|
Rusty Pipes
|
 |
« Reply #9 on: April 30, 2017, 01:25:01 PM » |
|
OK, I read all this a couple of times. I understand all this. All good info. I'll give it hell here in a few minutes. I'll keep yinz posted. Thanks
|
|
|
Logged
|
|
|
|
Rusty Pipes
|
 |
« Reply #10 on: April 30, 2017, 03:40:31 PM » |
|
Well, nothing was working. I put a block under the impact socket and stepped on the cheater/breaker bar. No joy but the axle bolt was about shot so I got out the Milwaukee drill. I drilled a 1/4" hole clear thru the bolt. Unfortunately I was not true with the axle center line so the bit broke off as I busted thru. Bit hit the inside of the axle and snapped.  I was able to drive the busted bit out of the bolt buy using an SS welding rod as a punch from the left side of the axle. Next i used a 3/8 bit, when I got in about 3/8" the head of the bolt popped off!  I then pulled the axle and chucked it in a V block on the arbor press. Stuck an easyout in the bolt end and to my amazement, it spun right out of the axle just using fingers only!! I am a 280 lb construction worker, not a whimp. I have no idea why this MFer would not come out, there was no rust on bolt, but it's out now. I believe Honda specs 62 Ft Lbs on that axle bolt. I think I'll go with Never Seize and 30 Ft Lbs when she goes back together. That axel can't move with the fork clamps anyway. No need for it to be that tight IMO. OK, Thanks for all the fine ideas on this folks. Next ...Timing belt replacement right after a BEER!
|
|
« Last Edit: April 30, 2017, 03:47:39 PM by Rusty Pipes »
|
Logged
|
|
|
|
The emperor has no clothes
|
 |
« Reply #11 on: April 30, 2017, 03:54:00 PM » |
|
I think I'd stick with the 62 lbs. I don't know why it gave so much trouble, but I'm pretty sure it wasn't from 62 lbs. of torque.
|
|
|
Logged
|
|
|
|
Hook#3287
|
 |
« Reply #12 on: April 30, 2017, 04:40:27 PM » |
|
I think I'd stick with the 62 lbs. I don't know why it gave so much trouble, but I'm pretty sure it wasn't from 62 lbs. of torque.

|
|
|
Logged
|
|
|
|
Blackduck
|
 |
« Reply #13 on: April 30, 2017, 05:09:18 PM » |
|
If you are going to used Anti Seize on the threads you need to drop the torque around 15-20% or you will over torque the fasteners. Have never had any problem crack out any threads using the lowest grade Loctite, the same way Honda assembled these. Loctite not only holds the fasteners but seals out moisture so no corrosion and stuck threads. Cheers Steve
|
|
|
Logged
|
2001 Standard, 78 Goldwing, VRCC 21411
|
|
|
Cracker Jack
|
 |
« Reply #14 on: April 30, 2017, 05:27:17 PM » |
|
Lefty loosely! 
|
|
|
Logged
|
|
|
|
da prez
|
 |
« Reply #15 on: April 30, 2017, 05:30:16 PM » |
|
Blackduck , please explain why you would reduce the torque when using anti-sieze. Nosey old mechanics want to know.
da prez
|
|
« Last Edit: May 01, 2017, 06:24:49 AM by da prez »
|
Logged
|
|
|
|
..
|
 |
« Reply #16 on: April 30, 2017, 06:44:26 PM » |
|
Blackduck , please explain why you would reduce the torque when using anti-sieze. Noaey old mechanics want to know.
da prez
Cause it makes it easier to over tighten by hand cause the anti seize acts as a "lubricant" making it easier to "crank 'er down."
|
|
|
Logged
|
|
|
|
Rusty Pipes
|
 |
« Reply #17 on: April 30, 2017, 07:18:36 PM » |
|
Yes, that is absolutely right. I did research on the Anti Seize vs torque thing 2 yrs ago. What I found was a 20-30% reduction in torque value was needed with anti seize vs dry thread so as not to exceed fastener stress levels. I posted my findings on GoldwingDocs and basically got laughed at. And no, I was not turning the bolt the wrong way! I have been working on bikes, boats, cars, steel mills and nuclear power plants all my life.
|
|
|
Logged
|
|
|
|
..
|
 |
« Reply #18 on: April 30, 2017, 07:20:51 PM » |
|
Rusty let us know what you think caused the problem once you've had time to mull it over for a day or two.
|
|
|
Logged
|
|
|
|
Blackduck
|
 |
« Reply #19 on: May 01, 2017, 03:38:13 AM » |
|
Loctite did publish an article explaining this, along with comparisons to dry threads. oiled etc. Would have to go rummage in my old Auto Engineering magazine collection and see if I can find it. Standard Loctite is similar to oiled threads for the purpose of torqueing fasteners. Cheers Steve
|
|
|
Logged
|
2001 Standard, 78 Goldwing, VRCC 21411
|
|
|
longrider
|
 |
« Reply #20 on: May 01, 2017, 07:19:58 AM » |
|
I"ve been in your shoes. Back in 98 I had the dealer install my first front. They must have had the inpact set to max. Just a bit of anti seize is good. Who installed the axle last? Galvanic action causes the treads to have a small amount of white dust, as I call it anyway and it becomes seized. I don"t use a torque wrench. Just nice and snug and you"re good to go
warren
|
|
|
Logged
|
|
|
|
falconbrother
|
 |
« Reply #21 on: May 01, 2017, 10:43:00 AM » |
|
I think of all the automotive/motorcycle issues that get me to cussing it's this stuff..  The older I get the less I cuss..but this kind of a thing.. I bought this old Suburban 1500, 4x4 with the 5.3 and the 4L60e transmission. The pan on that tranny has the worst drain plug design one can imagine. I rounded it off like 100% of the population..no big deal...I saw that coming. I pulled the pan and welded a nut on it. Broke that off. Grabbed an 8 inch long bolt and welded that thing on there for keeps and it was all I could do to break the drain plug lose with the bolt as a handle and a 2 foot long cheater bar. Was worried that I would warp the pan. I ground the top of that plug off and welded an 11/16 nut to it. Now I refrain from over tightening and do regular drain and fills with the Dex-6. On my wife's old Sportster I was always having to work on it and always having to drill out and or split nuts. Of course it was a 1993 model.. I will say that when I did the rear brakes on the old Suburban I could not break those caliper bolts lose. I hit them with a torch and got them hot and they came right out.
|
|
|
Logged
|
|
|
|
gordonv
Member
    
Posts: 5763
VRCC # 31419
Richmond BC
|
 |
« Reply #22 on: May 01, 2017, 09:38:35 PM » |
|
Yes, that is absolutely right. I did research on the Anti Seize vs torque thing 2 yrs ago. What I found was a 20-30% reduction in torque value was needed with anti seize vs dry thread so as not to exceed fastener stress levels. I posted my findings on GoldwingDocs and basically got laughed at. And no, I was not turning the bolt the wrong way! I have been working on bikes, boats, cars, steel mills and nuclear power plants all my life.
I watch the Spike TV auto shop shows, and that is exactly what the ARP bolts do when they add their "lubricant" to their bolts.
|
|
|
Logged
|
1999 Black with custom paint IS 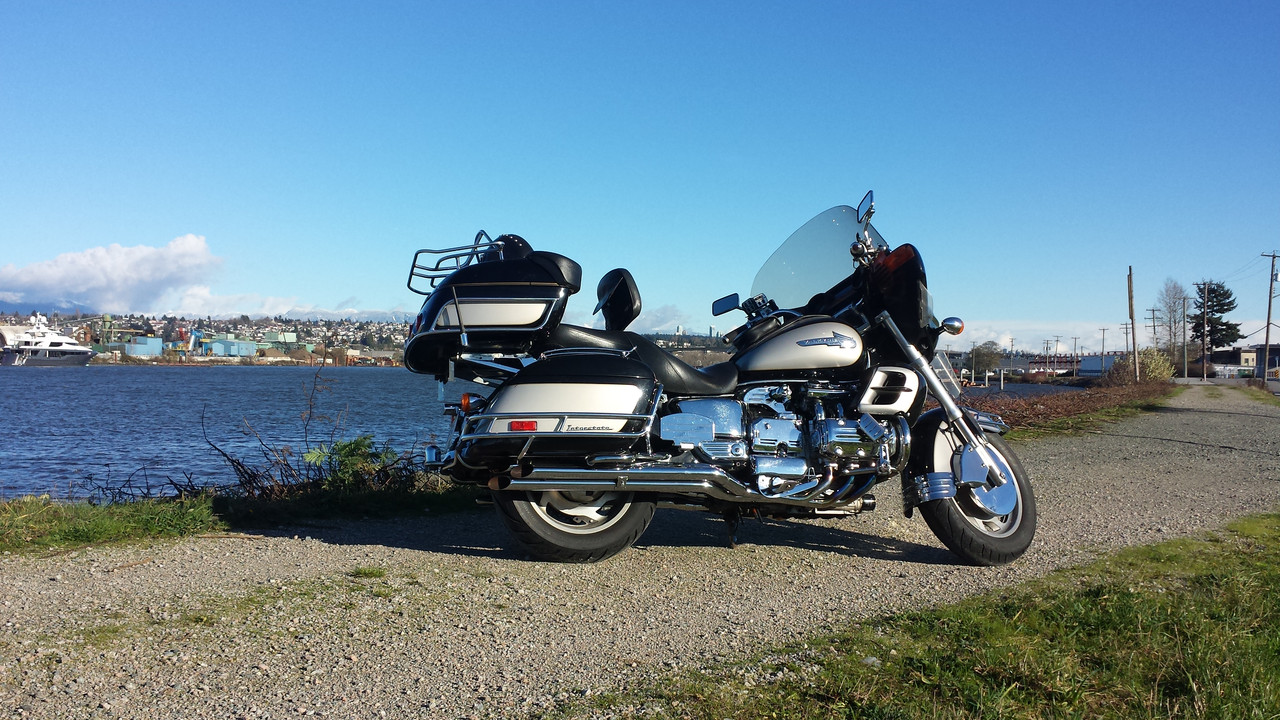 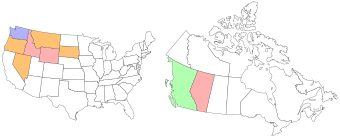
|
|
|
|